Технология, опередившая время | | |
Краткая характеристика на Wielarider + Schill InvertaSpot GT
Удовлетворяет всем современным требованиям автопроизводителей и кузовных цехов в отношении надёжности и эффективности. Аппарат с высокочастотной инверторной технологией предназначен для сварки современных сверхвысокопрочных и борсодержа-щих сталей (UHSS, USIBor). Рабочая частота аппарата - 10 000 Гц, номинальный ток сварки 13 000А, давление в точке сварки 650 даН. Омологирован многими автопроизводителями. Главная особенность аппарата - трансформаторные сварочные клещи С-образной конструкции. При использовании клещей этого типа потери мощности минимальны, поскольку преобразование происходит в самих клещах, а потребляемый ими ток не вызывает избыточного нагрева кабеля. Интеллектуальный контроль технологического процесса сварки гарантирует получение сварных точек, аналогичных формируемым в процессе производства автомобилей. Все данные по сварке сохраняются на карте памяти (SD-формат). Имеется возможность записи данных по параметрам 100 000 сварочных точек, что позволяет впоследствии контролировать качество ремонта. Возможна работа с оригинальными данными от производителя (OEM - программа). Если пользователь не может определить качество свариваемых сталей, существует уникальная и защищенная патентом программа тестирования материала. Возможно обновление ПО аппарата через карту памяти SD. Графический дисплей отображает параметры сварки в режиме реального времени по основным параметрам (кА, мсек, даН). Полное микропроцессорное управление позволяет исчерпывающим образом контролировать процесс сварки.
Другие особенности аппарата:
- индивидуальный выбор и установка параметров сварки; - автоматическое исправление неправильного хода сварки; - возможность сообщения о необходимости обслуживания насадок электродов; - вывод сообщений об ошибках в текстовой форме; - отображение типа наконечников электродов, которые могут использоваться; - распечатка результатов в формате А4; . - наличие центрального разъёма для подключения различных сварочных инструментов.
Магнитное поле данного оборудования имеет уровень намного ниже разрешённого предела, поэтому InvertaSpot GT работает с минимально возможным воздействием на организм человека.
Доступна версия для сварки алюминия с током сварки 20 000 ампер.
Аппарат может использоваться не только в кузовном ремонте, но и в производстве, где необходимо проводить качественную сварку. Оборудование может применяться при производстве автобусов, для односторонней сварки кузовных панелей.
Комментарии специалиста
Сварка - один из способов соединения деталей кузова автомобиля, применяемый на сегодня наряду с прочими, например, клейкой и клёпкой. И прошедший достаточно длинный путь совершенствования, отслеживающий, порой с опозданием, модернизацию конструкции автомобиля и обновление материалов, используемых в его производстве.
До недавнего времени именно сварка была фактически единственным способом соединения кузовных деталей без применения резьбовых вариантов крепления. Почему? Причина вполне прагматична и ясна: это быстро, технологично и просто. А также возможно в тех случаях, когда условия не позволяют работать, имея доступ к детали с обеих сторон.
Недостатки сварки проявили себя уже в первом поколении аппаратов для сервисного использования - газовых. Это коррозия по шву, грубый заметный след работы, ослабление материала. Проблемы серьёзные, и решать их было необходимо. В степени, достаточной для своего времени, это удалось благодаря внедрению нового типа аппаратов MIG/MAG, производящих сварку в среде инертного или неинертного газа. Швы стали аккуратнее, коррозионная стойкость выросла. И мастера ненадолго вздохнули с облегчением.
Именно ненадолго -ведь автопроизводители вступили в новую фазу борьбы за клиента. Автомобиль стало необходимо делать всё легче, динамичнее, экономичнее и экологичнее. То есть - перейти к применению прогрессивных материалов, не рассчитанных и в малой степени на старые сварочные технологии.
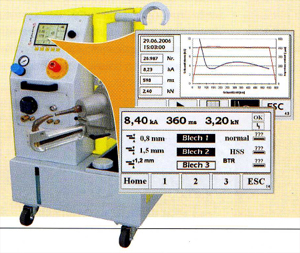 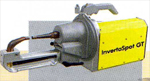 invertaSpot GT, его С-образные клещи и фотографии экрана.
Показатель |
мягкая сталь |
высокопрочная сталь |
Предел текучести |
120-180 H/mm |
200-700 H/mm |
Предел прочности |
440-470 H/mm |
500-1300 H/mm |
Относит. удлинение |
до 40% |
5-30 % |
В первую очередь речь идёт о высокопрочных сталях. При работе с ними сварка швами утратила всякую привлекательность. Ведь проявился её новый, критически опасный недостаток: изменение структуры металла в зоне воздействия высоких температур, ведущее к его переходу из категории высокопрочных в группы обычных сталей. А это -ослабление конструкции автомобиля, делающее его дальнейшую эксплуатацию после серьёзного ремонта опасной.
Шагом к решению проблемы стали аппараты точечной сварки, сводящие к минимуму опасное воздействие и сохраняющие прочность соединения высокой и надёжной. То есть по сути произошел переход от обычной и привычной сварки к более сложному процессу соединения при комплексном воздействии давления и тока. Иное решение - внедрение альтернативных технологий крепления: клейки и клёпки. Не только более сложных и затратных по времени производства работ, но и в корне отличных от заводского технологического цикла. То есть опять-таки заведомо не идеальных.
Но этот компромисс был неизбежен.
Ведь сегодня ремонтникам приходится иметь дело уже не только с высокопрочными сталями - то есть, например, имеющими маркировку HSS, - низкоуглеродистыми с добавлением таких легирующих компонентов, как марганец, ниобий, кремний. Но и с более «серьезными» продуктами, относимыми к группе сверх высокопрочных сталей, то есть борсодержащих.
 Слева направо: развитие технологий сварки, сокращающее зону ослабленого сплава
Если этой проблемы кому-то мало, есть и иная. Это необходимость соединять в целостный монолит по крайней мере три слоя различных материалов. Тонких, прочных, упругих, имеющих сложный профиль и несущих полную ответственность за жизнь и здоровье пассажиров при боковом ударе. Читайте тут: в случае низкокачественного ремонта эта ответственность может легко оказаться на плечах, а точнее, на бюджете, кузовного центра. И оказывается! Пока чаще всего - в Европе, но и отечественные страховые компании внимательно изучают все возможности сокращения своих затрат. Так что - клейте, клепайте, варите с неизбывным страхом перед не слишком порой оправданными и трудно опровергаемыми обвинениями.
Или примите как данность необходимость один раз оплатить ускорение процесса ремонта и свой финансовый покой, приобщившись к числу пользователей аппарата четвёртого поколения. Того самого, досье на который мы предложили в начале этой статьи.
Он, по сути, уже не имитирует заводские технологии, а реализует их в полном объёме, позволяя получить соединение, идентичное промышленному. И не только получить, но и иметь полную информацию по реальной оценке качества каждой точки. Ведь аппарат тестирует свою работу и сохраняет отчёт. Полный, являющийся достаточным доказательством для страховой компании. И основанием для начальника цеха или смены принимать автомобиль, не опасаясь подвоха со стороны нового или утомлённого за смену мастера.
Технология
На рисунке (вверху на этой странице) вы видите пример того, что может наблюдать пользователь нового аппарата. Это график. Он демонстрирует нам материалы, соединяемые в данном случае. И проводимый постоянно аппаратом контроль их существенных для работы параметров - изменения сопротивления, например. Для каждого материала имеются статистика и алгоритм, позволяющие не только определить точку плавления, но и «сместить» её во времени. Так, чтобы для всех трех материалов этот процесс начинался фактически одномоментно. То есть, с одной стороны, срок воздействия высоких температур свёлся к минимуму, а с другой - сварка оказалась наиболее успешной и надёжной. До сих пор такое было фактически недостижимо.
Но и это - не всё. Как уже сказано в «досье», аппарат самостоятельно тестирует качество каждой «линзы» и оценивает его в баллах, сохраняя полную информацию в файле отчёта. То есть создает достоверную и объективную картину качества проведённого ремонта и его соответствия заводским стандартам. Именно заводским, - ведь аппарат омо-логирован ведущими автопроизводителями и имеет встроенную ОЕМ-програм-му, позволяющую ремонтнику использовать из базы данных аппарата полную информацию по материалам в зоне сварки конкретной марки и модели автомобиля.
Это даёт возможность работать с полноценной технической поддержкой. Компания «Интерколор» - это единственный сертифицированный дистрибьютор Wielander + Schill на территории России. Интерколор проводит обучение работе на данном типе оборудования и осуществляет техническое обслуживание и при необходимости ремонт.
На фотографии рядом с графиками представлен типичный пример работы InvertaSpot GT. Это одна из стоек - передняя, средняя или задняя. Два слоя стали «узи-бор», и третий - более стандартная высокопрочная сталь. Толщина тоже типична, порядка 1,5 мм. Сварить их между собой достаточно трудно, ведь необходимо обеспечить монолитное соединение для различных составов сплава и условий прогрева.
Центральный слой будет получать совершенно иное воздействие, нежели крайние.
Как добиться высоко качества «линзы», то есть зоны соединения? Попытаться подобрать силу сжатия материалов, ток и длительность воздействия, наиболее подходящие для данного случая.
В аппаратах с Х-образными клещами проблемы «стартуют» с момента выбора режима. Ведь прижимающая сила в точке сварки заведомо не постоянна и зависит, что очевидно из правил элементарной механики, от плеча, - то есть длины электродов. Да и подаваемый ток не стабилен.
Даже мастер высокой квалификации не может определить качество сварной точки, выполненной сварочным аппаратом в каждом конткретном случае. Усилие на разрыв точки можно определить, только проведя необходимые исследования, а эта возможность отсутсвует у работников кузовных цехов. InvertaSpot GT осуществляет самостоятельный контроль процесса сварки, а соответственно и качественные показатели точки.
А продолжаются сложности в различных случаях по-разному, но одинаково неприятно. Здесь и громоздкий трансформатор, «выдающий» до 60 000 А, расходуемые на пять шестых (!) на потери, и силовые кабели, которые греются и собирают на себя весь металлический сор в помещении. И магнитные поля огромной мощности, далеко не полезные для здоровья людей.
InvertaSpot GT решает большую часть перечисленных проблем. Например, до появления аппарата Meredes допускал для ряда моделей в ремонте наиболее ответственных с точки зрения безопасности зон (стоек) лишь клейку и клёпку. Теперь же ситуация изменилась, разрешена сварка указанным аппаратом.
Более того, ряд производителей сейчас намерен серьёзно пересмотреть требования к оборудованию кузовного участка в сторону их ужесточения, поскольку безопасность и жизнь пассажиров - неоспоримый приоритет для них. С этой точки зрения ремонт, не создающий в дальнейшей эксплуатации потенциальных угроз, - достойная визитная карточка для любой компании, декларирующей стиль уважительного отношения к клиенту.
Издание: ПРАВИЛЬНЫЙ АВТОСЕРВИС Оксана ДЕМЧЕНКО
|